Maximizing Productivity from your Carbide End Mills is MUST for shop floor's to Improve there Profitability in the Competitive Environment
We've all heard about how important it is to have good Solid Carbide Tools. The same goes for Solid Carbide End Mills they make a huge difference in the quality of your work and can make the difference between a successful project and an unsuccessful one. But which one is the best? In this article, we'll explore some of our favourite carbide end mills available today, including their strengths and weaknesses as well as their applications. We'll also go over some tips and tricks for getting the most out of your solid carbide end mills so that your TEAM can achieve Targeted CPC (Cost Per Component) for your component so that you can WIN Over your Competition.
Introduction to Carbide End Mills
Carbide end mills are a type of tool designed to cut and machine metal. They're used in many industries, including automotive and aerospace, where they're used to manufacture parts that require high-precision machining.
Geometry & Angles of Carbide End Mills
The geometry of Carbide end mill is a critical aspect of its performance, since it determines how much material it will cut in one pass. The angle at which you feed your end mill (the tool's angle on the surface of your workpiece) and its radius determine how fast and deep this cut will go, as well as its effectiveness at removing material from the part being machined. A shallow angle will produce light cuts while still allowing some material to be removed; a steep angle results in deeper cuts that can remove more metal than lighter cuts would allow.
Different Coatings on Carbide End Mills
Carbide end mills are coated with a thin layer of coating material mainly by Two processes namely, PVD (Physical Vapour Deposition) or CVD (Chemical Vapour Deposition) to improve their cutting performance, durability and tool wear. Commonly used coatings include:
- TiAlN / FUTURA (Titanium Aluminium Nitride) : This is most versatile coating used in industry these days as it can be used for variety of materials to machine from Steel to CI to SuS to Titanium etc.
- TiN (Titanium Nitride) : This is yellow color coating avaialble in both PVD & CVD versions, CVD versions are mainly used for Inserts in roughing applications ; whereas in Carbide End Mills mainly PVD version is used as these end mills are mainly for finishing applications. This coating is used for variety of material machining from Steel, Cast Iron etc.
- AL-PRO (Alchrona Pro, ) : AlCrN-based all-rounder coating for cutting, punching and die casting, This is Bright Grey in colour. This results in an extremely wear resistant coating with excellent hot hardness and thermal shock stability. In short: The universal coating for superb results in dry and wet machining at high cutting speeds. Maximum Service Temperature of ~500*C.
- NOVA : Combination of AlTiN-based and TiSiXN layers gives high resistance to abrasive wear resulting in longer tool service life. This bronze colour coating can have maximum service temperature of ~1000*C
- Hard Carbon Coating, DLC (Diamond Like Coating), ZrN : Especially meant for Aluminium Machining or Non-ferrous Material machining.
- In Image Below different coatings are depicted offered by Rohit Cutting Tools namely from left: Uncoated , TiN, NOVA, Uncoated, TiAlN, NOVA, AL-PRO

Best Practices for your Carbide End Mills
- The first on my list is Machining Centre (VMC) itself, in High Performance Milling the Machining Centre is the most important part. Check the machining centres are of best quality with Strong Rigidity, Least Spindle Run-out, High Coolant Pressure. Machines are like humans if you pamper them they will give you the best results in your relationships; so do not forget to pamper your machines with the best coolant, regular maintenance checks & also best environment.
- Holding system plays important role in reducing the Tip Indicative Run-Out ( TIR ). So always use Hydraulic or Shrink Fit holding systems for best results.
- Importance of TIR Machinist across the world will second the Studies findings that for every increase in TIR by 0.010mm i.e. 10 Microns increase in TIR results in reduction in life by 10% and this factor is Exponential in nature. It means that if High Performance Carbide End Mills cost you say $50 it will give you result of $40 and will decrease substantially to even lower than say $10 with increase in run-out to 50-microns TIR.
- Coolant & its pressure Studies shows that a good quality coolant can increase the life of the tool by at least 60%. Hence using quality coolant with right mix & right pressure is a must. For checking the right coolant mix you can use Refractometer (How to use refractormeter)
- Clamping Fixture should always be hydraulic , avoid the use of manual fixtures with tightening screws/bolts as it may cause the failure of high performance tooling and will also lower your productivity considerably as you may encounter noises & poor finish due to the poor fixturing.
- Select RIGHT Carbide End Mills for the JOB i.e. as perr material to machine: So if you want to machine Alloy Steel Or Stainless Steel or Titanium then you can go for our 322 Series Or Variable Helix End Mills 330 Series or Variable Helix 5Flute 333 Series . For Machining Aluminium you can go for higher helix Carbide End mills like 211 Series & 213 Series from ROHIT's
- Selecting RIGHT Parameters for your End Mills, for this always go through manufacturers catalog for starting parameters for your Carbide End Mills.
- Feeding It Too Little or Too Much : Its like your own stomach if you FEED it too much or TOO Little there is bound to cause problems. So always follow manufacturers FEED & SPEED Starting Points .
- Selecting Right Number of Flutes
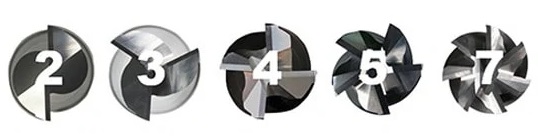
- Always select the shortest flute length Carbide End Mills for best rigidity and better life. Do not go for long flute lengths Carbide End Mills in order to get maximum regrinding { you know what I mean, every machinist in his/her endeavour to reduce tooling cost invariably tries to use higher flute lengths & finally screws it up....:) } As this leads to premature breakage of Carbide End Mills and hence your tooling cost goes up considerably; leaving you to close your projects due to over expenditure on the tooling.
- Shorter flute length / Optimal Flute Length for your Carbide End Mills will also mean that you can run them at HIGHER parameters and achieve better life from your End Mills.
Conclusion
- To get best results of your Solid Carbide End Mills / Cutting Tools make sure your TIR < 10 microns
- Always do maintenance of your machine Spindle on regular intervals
- Running It Too Fast or Too Slow Can Impact Tool Life , so PARAMETERS are KING , so always check with manufacturers catalogue for right starting parameters.
- Select the Shortest Possible Flute Length Carbide End Mills for the job
- Keep the minimum Overhang of the Carbide End Mills to prevent premature breakage of the tools.
- Select the right Tool Path for your job i.e. Interpolation , I-Machining , High Speed Machining, etc.